Barthel Group chooses Martin Automatic - for non-stop operation of its narrow web presses'
Posted: April 03, 2023
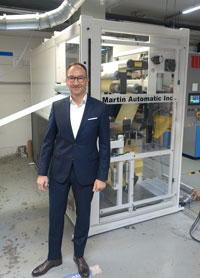
The Martin Automatic LRD rewinder - 'there is no future here for a label press without automatic roll handling', said Mr. Mischa Barthel
Leading German based label converter, Barthel Group, has installed more Martin Automatic technology at its production facility in Essen. The latest Martin machines are an MBS non-stop unwind/splicer and LRD automatic transfer rewinder fitted to a Nilpeter FA5 flexo press. Last year, Barthel also installed Martin MBS machines on two Mark Andy Evolution 5 presses at its atb plant in nearby Herne. According to Group Managing Director, Mischa Barthel: "Non-stop operation of narrow web technology is the only way to maximise productivity - there is no future here for a label press without automatic roll handling."
The Barthel Group, which was established in 1984 by Joachim Barthel and Detlef Klusmann, currently employs more than 500 people across its six sites, and its €110m/year turnover makes it one of the largest privately owned label converters in Europe. Now under second generation management with Mischa, Joachim's son, at the helm, today's set up includes the parent plant in Essen, Barthel Digitalprint, and acquisitions DES, evert, eprint, and atb in Germany as well as KIEN in the Netherlands. In all, more than 50 printing presses are in daily production with each plant specialising in certain products for different sectors but also offering the Group spare capacity during busy periods or during breakdowns.
But this is a far cry from how it all began with two-colour and four-colour Webtron water-based flexo presses to comply with the food industry regulations. The company eventually moved into UV-letterpress and subsequently UV-flexo, UV-offset and digital in the early 2000s. Mischa Barthel started helping at the factory from the age of 13, and later, having worked his way up through all the company departments, took over as Managing Director in 2008. It was his experience with an Arsoma TR rewinder fitted to one of the Webtron presses that demonstrated the value of automation, and this principle has been kept firmly in mind for all subsequent investment in new press technology.
"We chose Martin Automatic as our preferred supplier because of its established reputation in the narrow web market - the Martin name appears to be synonymous with reliability and performance, and we had no doubt that it would make a significant impact on our production floor," said Mr Barthel. As well as saving time, material, and the physical effort involved with roll changing, the Martin Automatic machines allow the presses to run at consistently higher speeds with none of the print quality variation that is caused by ramping up and down to change rolls manually. "As well as improving productivity and showing a fast ROI, the Martins have had a motivational effect on the production teams, who now deliver a higher volume of saleable product with less physical effort," he added.
The two latest Martin machines are an MBS non-stop unwind/butt splicer and an LRD rewinder. The MBS features built-in roll loading for rolls up to 455kg. It has a maximum splicing speed of 150m/min, a maximum web width of 560mm and can handle rolls up to 1016mm in diameter. The splicer monitors the remaining diameter of the roll and automatically splices to the new roll at a pre-set diameter. The MBS is followed by a festoon that has Martin's patented inertia compensation technology for consistent and accurate tensioning of the web throughout the process. The LRD rewinder, which matches the capability of the MBS, is fitted with two spindles and unloads finished rolls up to 800mm in diameter automatically onto the integral ramp. It is designed to minimise cycle time and delivers rolls to specific customer requirements.
Today, Barthel's product range includes labels for the food, wine, and beverage sectors, as well as fabric and homecare, cosmetic and personal care, pharmaceutical, logistics, and industrial products - a broad and highly sustainable base for the business. The Group utilises a range of print technologies from toner-based digital to inkjet/flexo hybrid, offset, UV-flexo and flat-bed screen. One might say it has all bases covered! Materials used are all in line with its mantra of sustainability, so include PCR substrates, detach adhesives, FSC certified materials or compostable solutions.
What of the future? "We intend to diversify our operation and gain a footprint in new markets and different geographic regions, especially Eastern Europe. I believe digitalisation and automation are the way forward and our future investments will reflect this - cost control and improved efficiency and speed to market are key. The challenge is to keep the success going by adapting to market conditions!" he concluded.